On a social media site, a question came up about how to accurately figure out the minimum blank size required for a given spectacle order. The person inquiring was aware of a few different formulas, and wondered;
a) Why there were more than one?
b) Which would be the most accurate?
c) What’s the right way to do it?
It’s important to understand that the “formulas” mentioned for figuring minimum blank requirements for a given spectacle order are approximations, or “rules of thumb.” Most of these involve starting with a Frame Effective Diametre or frame E.D., which is, in fact, difficult to measure with a ruler, and which may not be useful in determining the actual requirement. The most common I’ve come across is, “measure the E.D. and add the decentration,” which would hardly ever be accurate. There is not a simple formula for accurately determining the minimum blank required.
“Even if all of them are available, it’s unlikely that anyone (at least anyone without some remarkable mutation) would be able to figure this out without a properly-programmed computer. It takes an algorithm.”
This is because determining minimum blank size accurately requires several data elements, many of which may not be available to a dispensing optician. Even if all of them are available, it’s unlikely that anyone (at least anyone without some remarkable mutation) would be able to figure this out without a properly-programmed computer. It takes an algorithm. First, we need a tracing, which usually consists of some number of radial measurements (typically 400 to 1000 radii), starting at zero degrees and proceeding counter-clockwise.
Note: If we don’t have a tracing, we’re in the domain of gross approximations, and none of the rest of this post will be useful.
The second dataset required is how much the lens blank, whether surfaced or cast in finished form, will have to be decentered at finish layout. That second dataset is the complicated part due to the magnitude and direction of decentration depends on the location of the Layout Reference Point (LRP) on the blank. For finished single vision lenses, the LRP is the Prism Reference Point (PRP), which is almost invariably coincident with the lens’ optical centre and the geometric center of the blank. For anything else, it’s more complicated. The LRP can be intentionally located essentially anywhere on a surfaced single vision blank. For segmented multifocals, on which the LRP is the segment, and traditional (cast) progressives, on which the LRP is the Fitting Cross, the LRP is “fixed” on the blank.
The dispenser may not have visibility, in the first instance, to what blank will be used to fabricate a particular order, and even if he knows that he may not know the configuration of the blank (that is, where on the blank the LRP is located). For freeform lenses, whether the LRP can be freely moved around on the blank, always within certain limits, depends on the Lens Design Software used.
Some designers don’t do this at all, while some allow it but only on certain designs, and others allow it on all designs. These characteristics, too, may not be easily ascertained by the dispenser. If we know all of the data points (something that we have to know when using our lab management software), we can figure out or specify the configuration of the LRP on the blank, and therefore, how the blank will have to be moved off-center when blocked or otherwise positioned for edging.
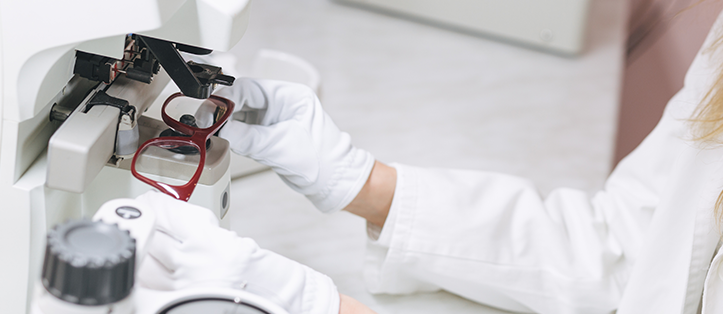
Given that datum – the blank decentration required – we can recompute the radii of the tracing, which are originally “centered” (meaning, the origin of the radii is located at the geometric centre of a circumscribing box) by moving the origin to the location of the center of the blank as decentered. This is where the trigonometry comes in; the “rho-theta” (radius and angle) radii are converted to Cartesian coordinates, modified by the blank movement, and then converted back. Once that’s done, we have a tracing, the origin of which is coincident with where the center of the blank will be in the shape. The longest of these radii doubled is the “raw” minimum blank required.
To that value, we may add some “cushion” to allow for various kinds of “play in the joints” such as small anomalies around the edges of blanks or positioning errors that can creep in wherever positioning occurs. As if that weren’t enough, there’s another consideration, which we can manage in our software (quite possibly uniquely so, since I’m pretty sure I thought this up), but which can be less than intuitive. Intuitively, one might think that the smallest blank is achieved when the blank is not moved at all at finish layout – that is, whatever finish decentration is needed is present in the blank. And that would be true if shapes were completely symmetrical, which only happens with circles and ovals.
Even a “pure” rectangle or square would normally have some relief in the lower nasal corners, so as not to cut off the wearer’s air supply, and of course, most frame shapes are quite asymmetrical. And in the case of even slightly asymmetrical shapes, the point in the shape where the smallest blank would be achieved is not at the box center, but at the center of the smallest containing circle of the shape. Figuring that out takes a fairly complicated algorithm!
The difference between this “centroid” and the geometric center of the shape is usually pretty small. Still it can be a few millimeters, which could easily be the difference between needing a 65mm blank and a 70mm blank, given that blanks are fabricated in a scalar enumeration of sizes, such as, 65, 70, 75.
Now, I can’t do much of any of this in my head, which is one reason why I wrote software to do this kind of thing in the first place. As I suggested earlier, if you want to know an accurate minimum blank size for a job before you submit an order to a lab, you will probably have to rely on lab management software (shameless plug: like ours), or do a whole lot of work to create a program yourself. Some practice management software systems (second shameless plug: like ours) “talk” to our lab software to get these kinds of calculations done. If your PMS can’t do that, my recommendation is, just let your lab’s software figure it out.