Freeform: A Brief History - Part 2
In Part 1 of Freeform: A brief history, I covered some of the evolution of surfacing technology leading up the point at which freeform production became possible. I wrote about how surface generators became capable of producing surfaces that could be polished directly after generating without any intervening “fining” (a.k.a “smoothing”) steps. As I noted in Part 1, “cut-to-polish” systems were initially used to produce the same kinds of surfaces as had been made by prior technology, namely, spheres and tores.
Before cut-to-polish became possible, when people in the field saw the improvements in form accuracy and surface roughness that generators could produce, their thoughts went to what had theretofore been a kind of “Holy Grail”. What if progressive lens surfaces could be cut with these levels of surface quality, on the ocular sides of spherical, semi-finished lens blanks?
ECPs. In addition to the detailed initial conversation required to promote uptake, discussions at follow-up visits need to delve into areas such as treatment efficacy, compliance and retention.
"The principal attraction of such a capability was obvious: semi-finished single vision blanks were (and remain) very cheap compared to semi-finished progressive blanks."
The principal attraction of such a capability was obvious: semi-finished single vision blanks were (and remain) very cheap compared to semi-finished progressive blanks. Furthermore, the number of different semi-finished single vision blanks that would have to be kept in inventory (seven to twelve different base curves) would be a fraction (typically one-ninth, there being nine common add powers) of the number of different semi-finished progressive blanks that have to be kept (seven to twelve base curves times nine addition powers), if progressive surfaces of various adds could be produced on demand. In short, the principal advantage of such innovation was perceived to be financial. Freeform progressives would cost less to produce – maybe a lot less.
Two additional improvements were required to turn these aspirations into practical realities.
The first; while generators could cut polishable surfaces, the existing process employed laps (also known as “tools”) cut to spherical or toric curves. The corresponding spherical or toric surfaces on the lenses to be polished could be rubbed against the lap surfaces, with a slightly-abrasive polishing slurry and pad between the lens surface and the lap surface, in motions sufficiently complex and random as to avoid producing localized errors in the surfaces, which could otherwise arise from any irregularity in the lap or pad surface.
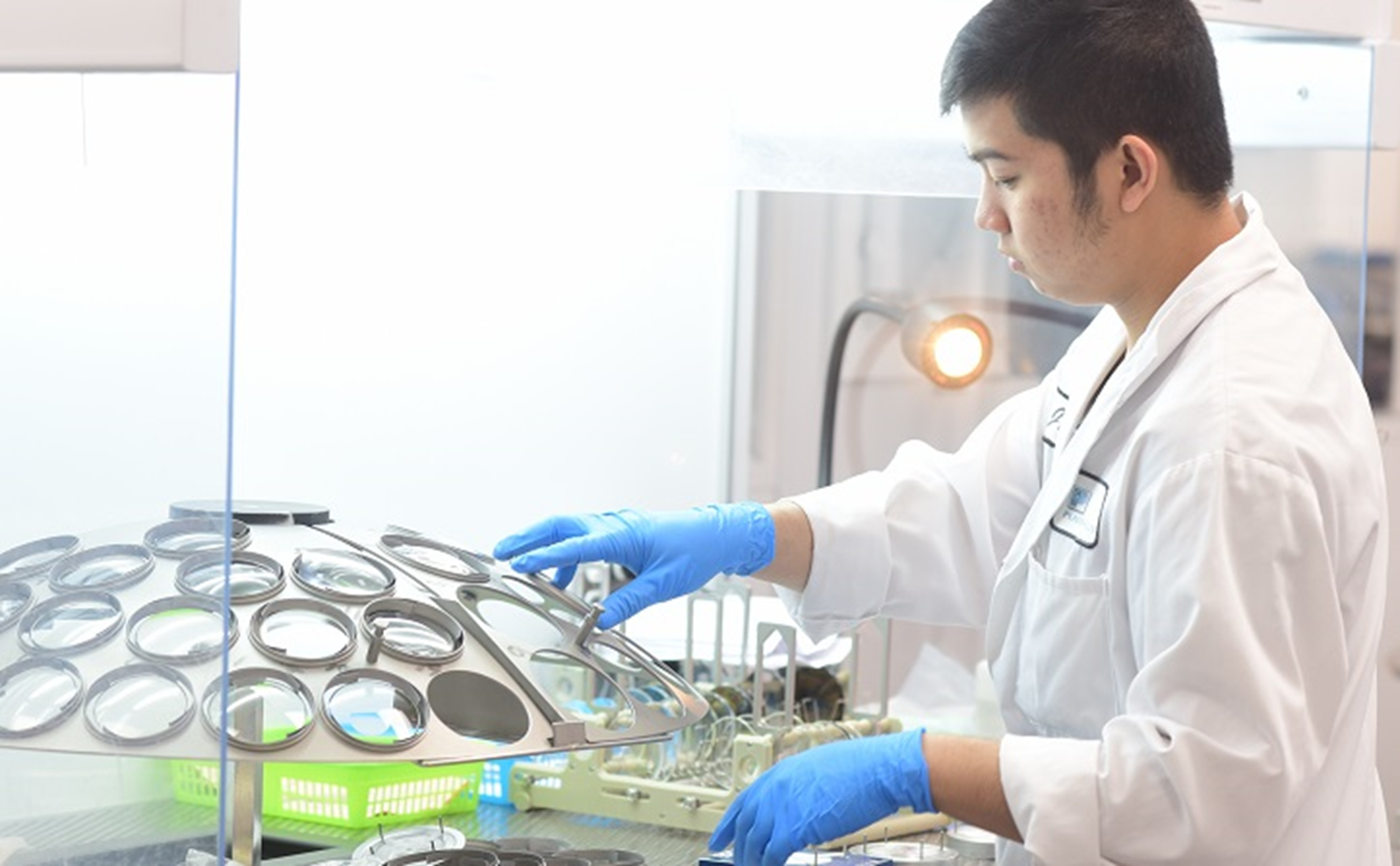
That kind of motion could not be used for a more complex surface, such as a progressive power surface. The undulations in the surface prevent the use of that rubbing motion. The solution turned out to be something quite simple: the use of “conformant” polishing laps, spun in machines that initially looked a lot like old fashioned “sphere” machines. The latter employed mushroom-shaped metal laps, spun on their “stems” (to stretch the metaphor); a lens held to the lap on one side of the lap, below its apex, would spin by virtue of the differing velocities of the spinning surface nearer to the center of the spinning lap, where the rotational velocity ultimately drops to zero, versus the outer edge.
The combination of the spinning lap surface’s curvilinear motion, the rotational spinning motion of the lens, and a third motion that moved the spinning lens across the surface of the lap from near the edge of the lap to near the center of the lap, produced a very efficient, randomized motion. Some of the earliest freeform polishers used that motion with a large, spherical lap, but a lap whose surface could conform to the irregular surface of the lens (hence, “conformant”). The conformant laps obtained their ability to conform to the undulating progressive surface from a layer of compressible material, not unlike a dense sponge, or foam, sitting between the base of the lap and the polishing pad. This layer allowed the lap surface to conform to the irregular (that is, non-spherical, non-toric, asymmetrical) lens surface throughout the process.
Further refinement of this process came in the form of so-called “small-aperture” laps, which were laps having diameters smaller than the lenses – on the order of one-third to one-half the diameters of the lenses. This required that the machines become more complicated to produce the motions needed to obtain an even, randomized treatment of the lens surface. However, the smaller diameter laps conformed better to the irregular progressive surfaces than the large ones could, so the small-aperture conformant laps have become ubiquitous.
"The surfaces themselves were unlike anything that had been produced commercially. Recall that the initial goal was to produce a progressive surface on the ocular (back) side of a semi-finished single vision blank."
The combination of generators capable of producing polishable surfaces, together with conformant-lap polishers made the manufacturing of complex surfaces on lenses practicable. However, an additional innovation was necessary to make the process practical. This was namely descriptions of surfaces that the generators, and to some extent, the polishers, could “understand”, to be able to produce the surfaces.
The surfaces themselves were unlike anything that had been produced commercially. Recall that the initial goal was to produce a progressive surface on the ocular (back) side of a semi-finished single vision blank. While it would have been possible to replicate a progressive design as had been produced on the object (front) side of progressive blanks on the back surface, it should be obvious that the progressive surface had to be combined with a “prescription surface” to provide usable lenses, and further, the combined surfaces would have to be adjusted to compensate for lens thickness and variations in the front surfaces of the blanks used. So, coming up with the desired surface required, and continues to require, individual calculation of the surfaces for each order.
Fortunately, early on in this process, a standard for communication between lab management software systems (“LMS”), lens design software systems (“LDS”), and freeform-capable equipment was created by extending the existing Data Communications Standard to accommodate the new data exchanges needed. The LMS could communicate with the LDS to obtain the surface design and deliver it to the machines when needed, and freeform technology became commercially practical, and eventually, mainstream.